How Does an Agitated Nutsche Filter Dryer Work in a Chemical Processing Unit?
- marketing43782
- Oct 2, 2023
- 2 min read
The Agitated Nutsche Filter Dryer is a workhorse in any chemical processing unit. It's important to understand that in the chemical industry, chemicals go through multiple stages to maintain product quality; they undergo processes for separating and isolating solids from liquid substances. The Agitated Nutsche Dryer, manufactured by Thermosag, finds its best use in pharmaceuticals, agriculture, dyes, colors, and pesticides.
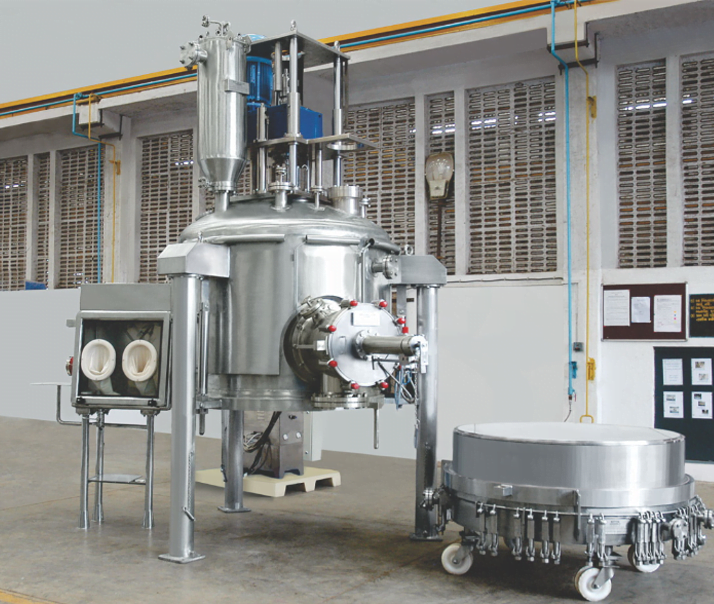
So, how does this multipurpose machine work? This multi-functional equipment can perform various operations in a single batch, including filtering, washing, re-slurring, and drying, all within a fully enclosed vessel. This blog delves into the process of the Agitated Nutsche Filter in a chemical processing unit.
Stage 1: Filtration with Agitator and Gas Pressure
The filtration process begins after placing the slurry or paste into a container or vessel. It starts slowly but with significant force to prevent clogging, which is called an agitation mechanism. Nitrogen gas pressure is used to conduct the effective separation of liquids and solids. The liquid passes through the filter cloth and is collected on the fiber plate, while the solids are retained within the filter cloth.
Stage 2: Cake Washing
Now that the liquid and solids are separated, the solids should be thoroughly washed to remove impurities. There are two common ways to conduct this cleaning process: the traditional wash method and the pre-slurry wash.
In the traditional wash method, a solvent is added to the crystals to flush out impurities or any traces of leftover liquid. This step is often repeated several times to achieve the best results. The Nutsche Filter has an advantage because it can smooth out the cake's surface before applying the spray wash, ensuring that the entire cake is washed evenly.
However, in the slurry wash method, a liquid (usually a solvent or cleaning solution) is sprayed or introduced onto a solid mixture known as a slurry. This liquid helps rinse or wash away impurities, contaminants, or unwanted substances from the solid particles in the slurry. As the liquid flows through the slurry, it picks up these impurities and carries them away, leaving behind cleaner, solid particles.
Stage 3: Drying
Once the washing has been completed, the drying process begins. There are two viable options that work best when heat moves efficiently and effectively through the container or vessel where the drying process is taking place: pressure drying and vacuum drying.
Pressure Drying:
In this stage, air or gas is used to remove moisture from the cake until it becomes very dry. To minimize moisture, the cake's surface is smoothed under pressure, sealing any cracks.
Vacuum Drying:
To further reduce moisture, the cake is broken up using rotating paddle arms. Applying heat to certain parts of the Nutsche Filter can enhance the drying process.
Stage 4: Discharging the cake
Once the washing and drying processes have taken place, the critical task of discharging the cake begins. There are several methods for this: central discharge with rotating paddle arms, auger arms, and side discharge, depending on the size of the machine.
In central discharge, the cake is continuously pushed toward the center.
Inside discharge, the cake comes out intermittently, not continuously, which requires additional planning for downstream equipment.
Conclusion
Get in touch with Thermosag to purchase an Agitated Nutsche Filter Dryer for your business. Their knowledgeable staff will provide you with thorough knowledge of the machinery and help you choose the best option for your business's requirements.
Comments